Understanding Pressure Measurement: Insights for Engineers and Technicians
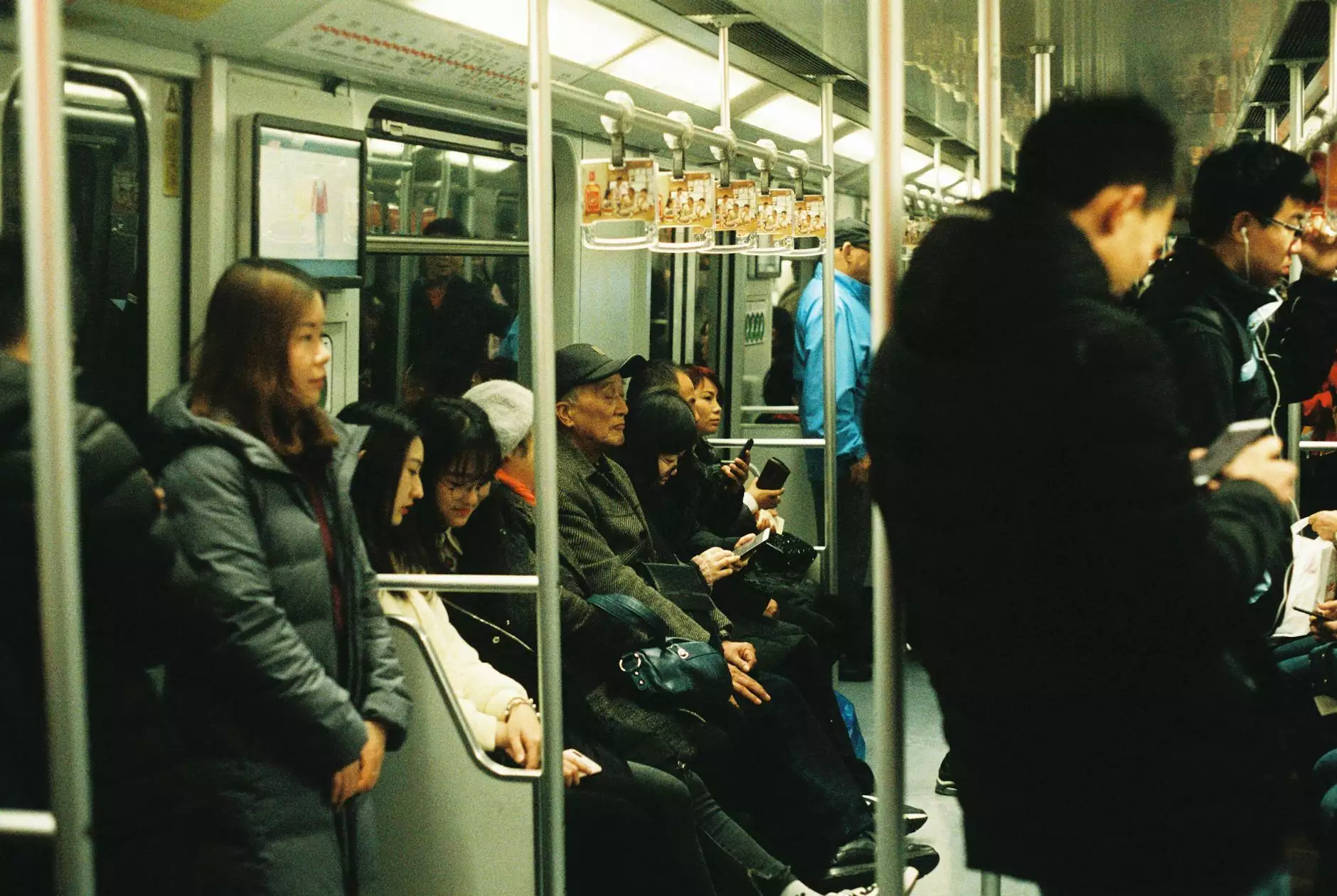
Pressure is a crucial concept in various fields, especially in engineering domains like auto repair, farm equipment repair, and structural engineering. Whether you are a seasoned professional or a novice eager to learn, understanding what pressure is measured in can greatly enhance your proficiency and effectiveness in your work. Let’s delve into the intricacies of pressure measurement, its units, applications, and significance in engineering practices.
What is Pressure?
Pressure can be defined as the force exerted per unit area. Mathematically, it can be represented as:
Pressure (P) = Force (F) / Area (A)
This fundamental definition is essential for understanding how pressure works in various engineering contexts.
Units of Pressure Measurement
When we talk about what is pressure measured in, we are essentially referring to the standard units that quantify pressure. There are several units of pressure used in different professions and contexts:
- Pascals (Pa): The SI unit of pressure. One pascal is equal to one newton per square meter.
- Bar: Commonly used in meteorology, one bar is equal to 100,000 pascals.
- Atmospheres (atm): Standard atmospheric pressure at sea level, approximately equal to 101,325 Pa.
- PSI (Pounds per Square Inch): Widely used in the automotive industry, particularly in tire pressure measurements.
- Hg (Inches of Mercury): Often used in weather reporting and barometers.
The Importance of Choosing the Right Unit of Pressure
Choosing the correct unit of measurement is vital depending on the context of the project. For example, when dealing with automotive repair, PSI is often preferred due to its practicality and ease of understanding for mechanics and technicians. On the other hand, engineers may prefer using pascals or bars when calculating stress in structures.
Measuring Pressure
Pressure can be measured using various devices. Understanding how these devices work and their appropriate application is crucial for accurate pressure measurement. Let’s discuss some of the most common pressure measurement devices:
1. Manometers
Manometers are simple devices used to measure pressure by comparing it to that of the atmosphere. A basic U-tube manometer consists of a liquid-filled tube. The pressure difference causes the liquid to move, and the height difference provides a measure of pressure.
2. Bourdon Gauges
Bourdon gauges are mechanical devices that consist of a coiled tube. When pressure is applied, the tube unwinds, and the movement is transferred to a needle that displays the pressure on a dial. These gauges are widely used in industries such as auto repair to measure tire pressure and in various equipment.
3. Digital Pressure Gauges
With advancements in technology, digital pressure gauges provide accurate readings using electronic sensors. They are often used in conditions requiring high precision, such as in laboratories or high-tech industries. Digital gauges can display pressure in various units and often feature additional capabilities like data logging and remote monitoring.
Applications of Pressure Measurement in Different Sectors
Understanding what pressure is measured in is crucial for its applications across various sectors, especially in farm equipment repair, structural engineering, and auto repair.
Auto Repair
In the auto repair industry, pressure gauges are essential for:
- Tire maintenance: Ensuring tires are inflated to the correct PSI for safety and efficiency.
- Fuel and oil pressure: Monitoring the performance of the engine and lubrication systems.
- A/C systems: Measuring refrigerant pressure to ensure optimal cooling efficiency.
Farm Equipment Repair
In farm equipment repair, pressure measurement plays a critical role:
- Hydraulic systems: Many farm machines rely on hydraulics, where precise pressure measurements ensure efficient operation.
- Irrigation systems: Monitoring water pressure to ensure proper flow in irrigation systems.
- Pneumatic tools: Ensuring pneumatic systems operate safely and effectively during repairs and maintenance.
Structural Engineering
In structural engineering, pressure measurements are applied to ensure safety and integrity:
- Soil pressure: Understanding how soil pressure affects foundation stability.
- Fluid pressures in structures: Evaluating the impact of water or other fluids on structural components.
- Load testing: Measuring how structures respond to varying pressure loads to ensure they meet safety standards.
The Future of Pressure Measurement
The field of pressure measurement is continuously evolving with technology. Innovations such as Internet of Things (IoT) sensors allow for real-time data gathering and analysis, enhancing the accuracy and reliability of pressure measurements across industries.
In the future, we can expect:
- Greater integration of sensors in machinery, leading to smarter equipment and predictive maintenance.
- Enhanced digital interfaces that allow for easier interpretation of pressure data.
- Automation of pressure control systems to improve efficiency in production environments and maintenance procedures.
Final Thoughts
Understanding what pressure is measured in is fundamental to the core functionalities across various engineering fields and industries. From auto repair to farm equipment management and structural integrity, accurate pressure measurement is paramount for safety, efficiency, and operational excellence. As technology advances, the methods and devices for measuring pressure will only become more sophisticated, allowing for improved practices and innovations in the engineering sector.
At Michael Smith Engineers, our expertise in pressure measurement is essential in delivering top-quality repair and engineering services tailored to your needs. Reach out to us today to learn how we can assist you in your engineering endeavors!